Scope of data calculation
The terms below are used to indicate the scope of calculation for the data provided.
- “SCI" indicates all facilities of Sanyo Chemical Industries, Ltd.
- “Domestic” indicates SCI plus domestic affiliates/subsidiaries ((1)-(4) and (10)-(12) in the graph below).
- “Overseas” indicates overseas affiliates/subsidiaries that have production facilities ((5)-(9)).
- For facilities with no notation, the scope is “domestic” plus “overseas.”
ISO Certification
*Horizontally scrollable
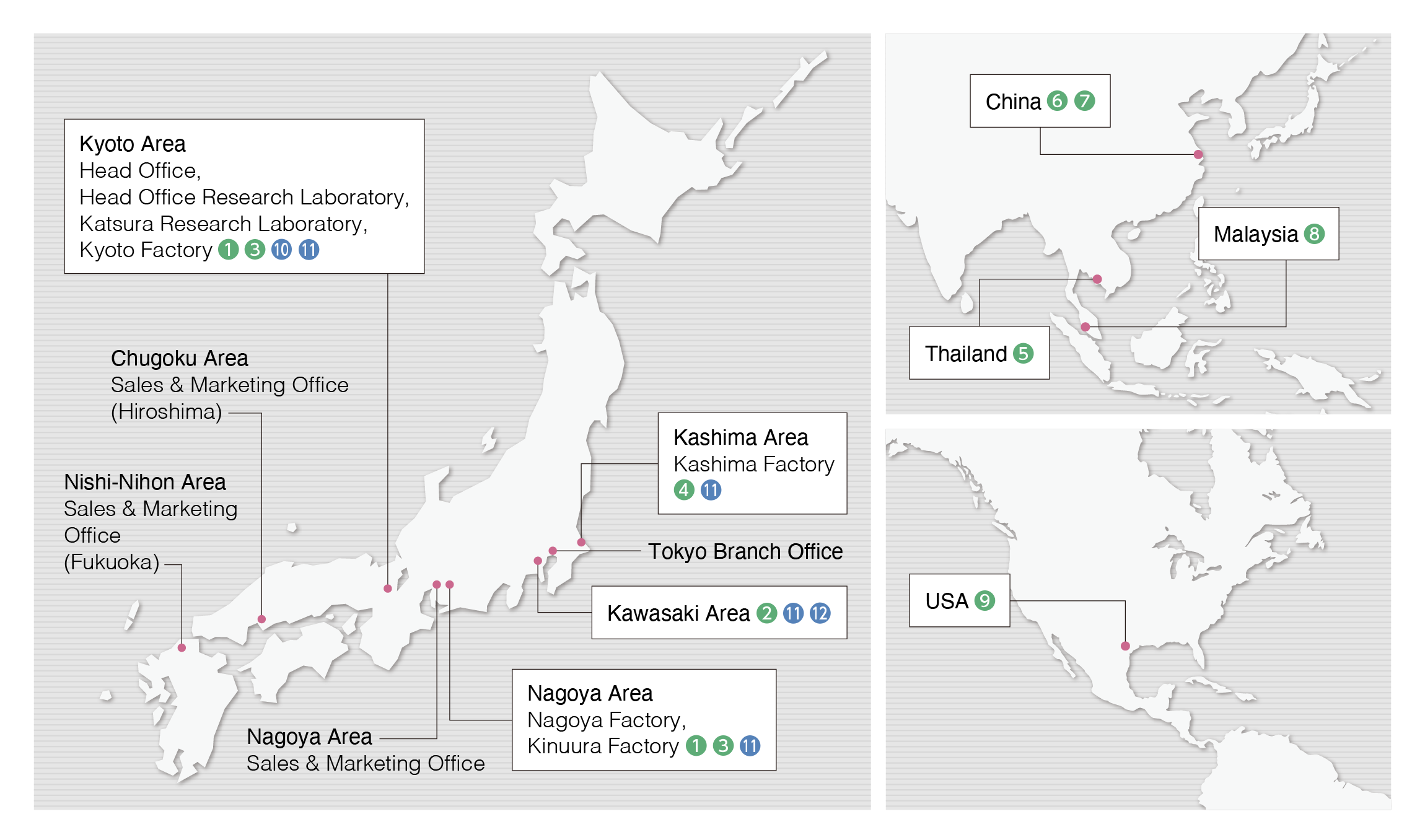
*Horizontally scrollable
Location | Facility | Year of establishment (operation) |
ISO14001 | ISO9001 | |||
---|---|---|---|---|---|---|---|
Year acquired | Certification authority | Year acquired | Certification authority | ||||
Production Base | - | Kashima Factory, Sanyo Chemical Industries, Ltd. |
1977 | - | - | 1997 | JCQA |
- | Kyoto Factory, Sanyo Chemical Industries, Ltd. |
1949 | - | - | 1999 | JCQA | |
- | Nagoya Factory, Sanyo Chemical Industries, Ltd. |
1969 | - | - | 1998 | JCQA | |
- | Kinuura Factory, Sanyo Chemical Industries, Ltd. |
2010 | - | - | 2010 | JCQA | |
(1) | SDP Global Co., Ltd. | 2001 | - | - | 2000 | JCQA | |
(2) | San Chemical Co., Ltd. | 1982 | - | - | 2000 | JCQA | |
(3) | SAN NOPCO LIMITED | 1966 | - | - | 2000 | JCQA | |
(4) | San-Petrochemicals Co., Ltd. | 1977 | - | - | - | - | |
(5) | Sanyo Kasei (Thailand) Ltd. | 1997 | 2009 | TICA/J-VAC | 2004 | TICA/J-VAC | |
(6) | Sanyo Kasei (Nantong) Co., Ltd. | 2003 | 2012 | TUV NORD | 2006 | TUV NORD | |
(7) | San-Dia Polymers (Nantong) Co., Ltd. | 2003 | 2013 | CQM | 2007 | DETNORSKE VERITAS |
|
(8) | SDP GLOBAL (MALAYSIA) SDN. BHD. | 2015 | - | - | - | - | |
(9) | Sanyo Chemical Texas Industries, LLC | 2005 | - | - | - | - | |
Non-production Base | (10) | San-Apro Ltd. | 1966 | - | - | 2003 | JCQA |
(11) | Sanyo Chemical Logistics Co.,Ltd. | 2020 | - | - | - | - | |
(12) | Shiohama Chemicals Warehouse Co.,Ltd. | 1983 | - | - | - | - |
-
The four Sanyo Chemical factories and domestic subsidiaries and affiliates (1) through (4) discontinued their ISO14001 certification in FY2020. (4) San-Petrochemicals Co., Ltd. also discontinued its ISO9001 certification in FY2020.
(1)(6)(7) and (8) decided to withdraw from the business in March 2024, and are scheduled to be dissolved or are under consideration for transfer (transfer of equity) accordingly.
Data Concerning Environmental Investment and Environmental Efficiency
Environmental accounting results
Trends in aggregate values by classification based on the Environmental Accounting Guidelines (2005 version)
Scope: Domestic and overseas
*Horizontally scrollable
Classification According to Business Activity
Investment/costs (unit: million yen)
Classification | FY2019 | FY2020 | FY2021 | FY2022 | FY2023 | |
---|---|---|---|---|---|---|
Facility area costs | (1) Pollution prevention costs | 172/872 | 260/843 | 216/842 | 297/875 | 164/884 |
(2) Global environmental conservation costs | 83/676 | 81/650 | 64/671 | 27/663 | 31/640 | |
(3) Resource recycling costs | 64/1,932 | 41/1,850 | 1/1,794 | 1/1,898 | 58/1,378 | |
Upstream/downstream costs | 0/30 | 0/34 | 2/40 | 0/33 | 0/32 | |
Administrative costs | 3/417 | 1/459 | 55/475 | 3/505 | 0/411 | |
R&D costs | 0/506 | 0/464 | 0/663 | 0/730 | 0/760 | |
Social activity costs | 0/138 | 0/124 | 0/132 | 0/138 | 0/154 | |
Environmental remediation costs | 0/3 | 20/5 | 0/3 | 0/4 | 0/3 | |
Total | 322/4,573 | 404/4,428 | 338/4,620 | 327/4,846 | 252/4,263 |
- Investment amounts are based on receiving inspections for the period in question. Cost amounts include depreciation.
*Horizontally scrollable
Classification According to Environmental Conservation Measures
Investment/costs (unit: million yen)
Classification | FY2019 | FY2020 | FY2021 | FY2022 | FY2023 |
---|---|---|---|---|---|
(1) Global warming measures | 65/675 | 40/633 | 19/646 | 34/642 | 37/630 |
(2) Ozone layer protection measures | 1/1 | 0/1 | 1/5 | 0/2 | 0/5 |
(3) Air-quality conservation measures | 65/395 | 185/394 | 232/391 | 224/408 | 136/407 |
(4) Noise and vibration measures | 3/73 | 5/75 | 1/64 | 0/74 | 0/70 |
(5) Environmental conservation measures for the aquatic, ground, and geologic environments |
98/426 | 136/414 | 73/432 | 62/456 | 44/446 |
(6) Waste and recycling measures | 69/1,940 | 34/1,857 | 1/1,803 | 1/1,906 | 58/1,383 |
(7) Measures for reducing chemical risk and emissions | 0/234 | 0/282 | 0/277 | 0/259 | 0/204 |
(8) Natural environment conservation | 10/19 | 0/16 | 3/17 | 1/16 | 0/12 |
(9) Other | 11/304 | 3/292 | 9/322 | 5/354 | 4/346 |
Total | 322/4,068 | 404/3,963 | 338/3,957 | 327/4,116 | 279/3,504 |
- R&D investment/costs are not classified
*Horizontally scrollable
Economic Impact of Environmental Conservation Measures (monetary units)
(unit: million yen)
Classification | FY2019 | FY2020 | FY2021 | FY2022 | FY2023 | |
---|---|---|---|---|---|---|
Energy savings | 81 | 6 | 41 | 20 | 26 | |
Resource savings | Waste reduction | 97 | 48 | 77 | 7 | 40 |
Raw material use reduction | 178 | 174 | 152 | 82 | 137 | |
Revenue from recycling | 80 | 52 | 55 | 70 | 78 | |
Total | 436 | 279 | 325 | 179 | 281 |
- Includes effects of non-investment measures (e.g., process improvements )
*Horizontally scrollable
Environment, safety, and accident prevention investment
(unit: million yen)
FY2019 | FY2020 | FY2021 | FY2022 | FY2023 | |
---|---|---|---|---|---|
Environmental conservation | 322 | 404 | 338 | 327 | 252 |
Safety/accident prevention | 425 | 344 | 391 | 611 | 719 |
Total | 747 | 747 | 729 | 938 | 971 |
Cumulative environmental investment (since FY2005)
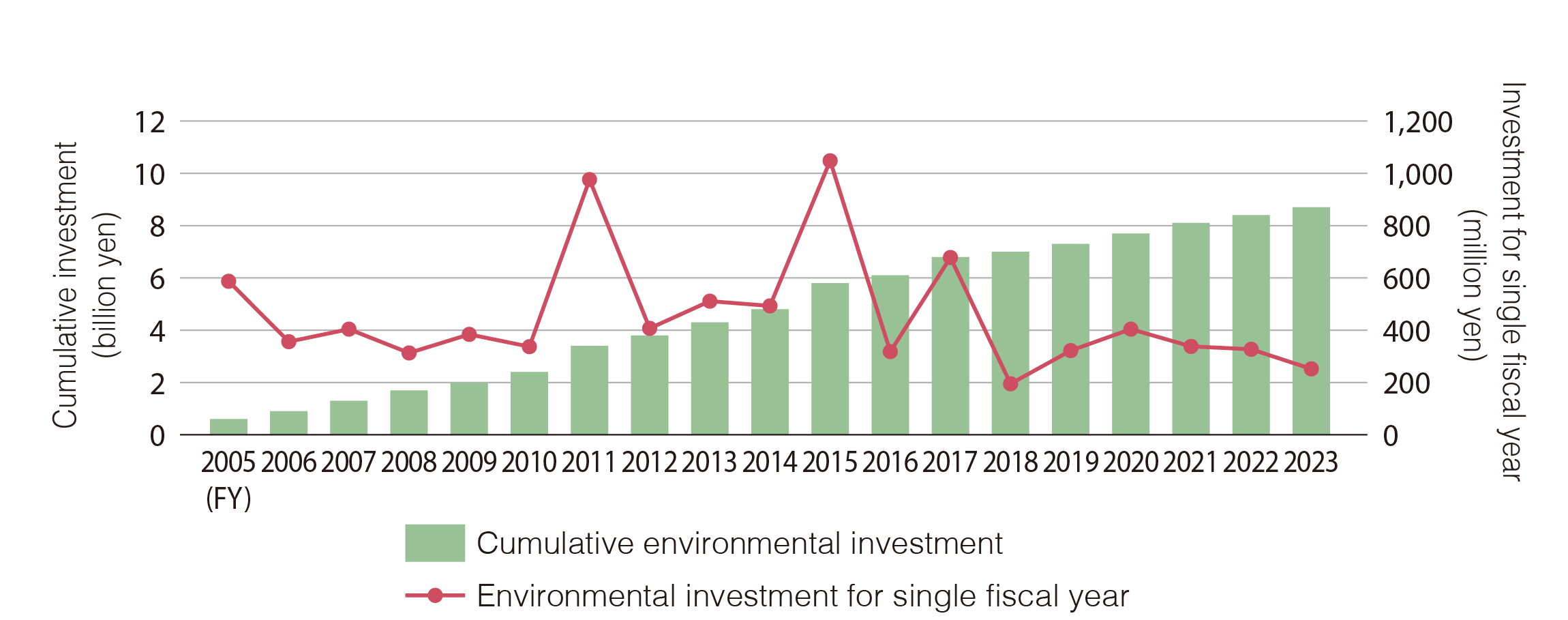
Cumulative safety/accident prevention investment (since FY2005)
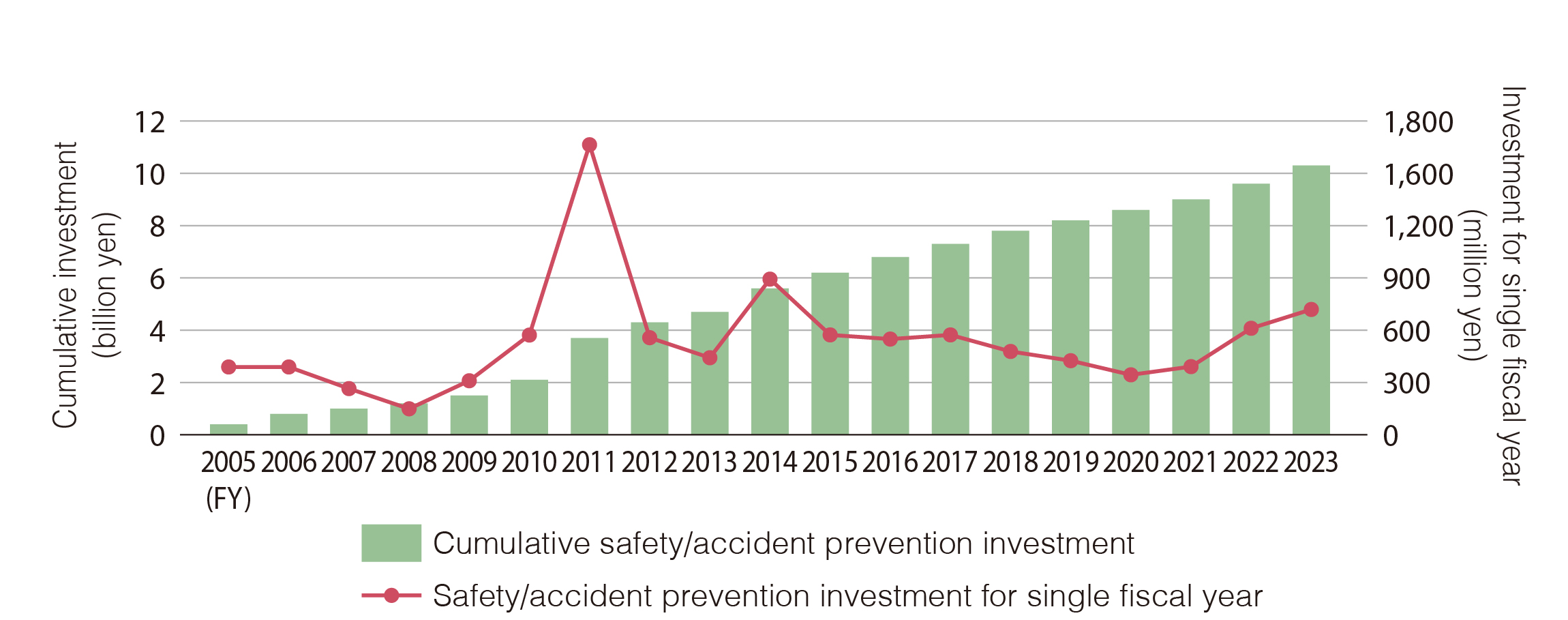
Environmental efficiency indicator (Japan Environmental Policy Priorities Index (JEPIX))
Environmental efficiency (JEPIX) (domestic sites)
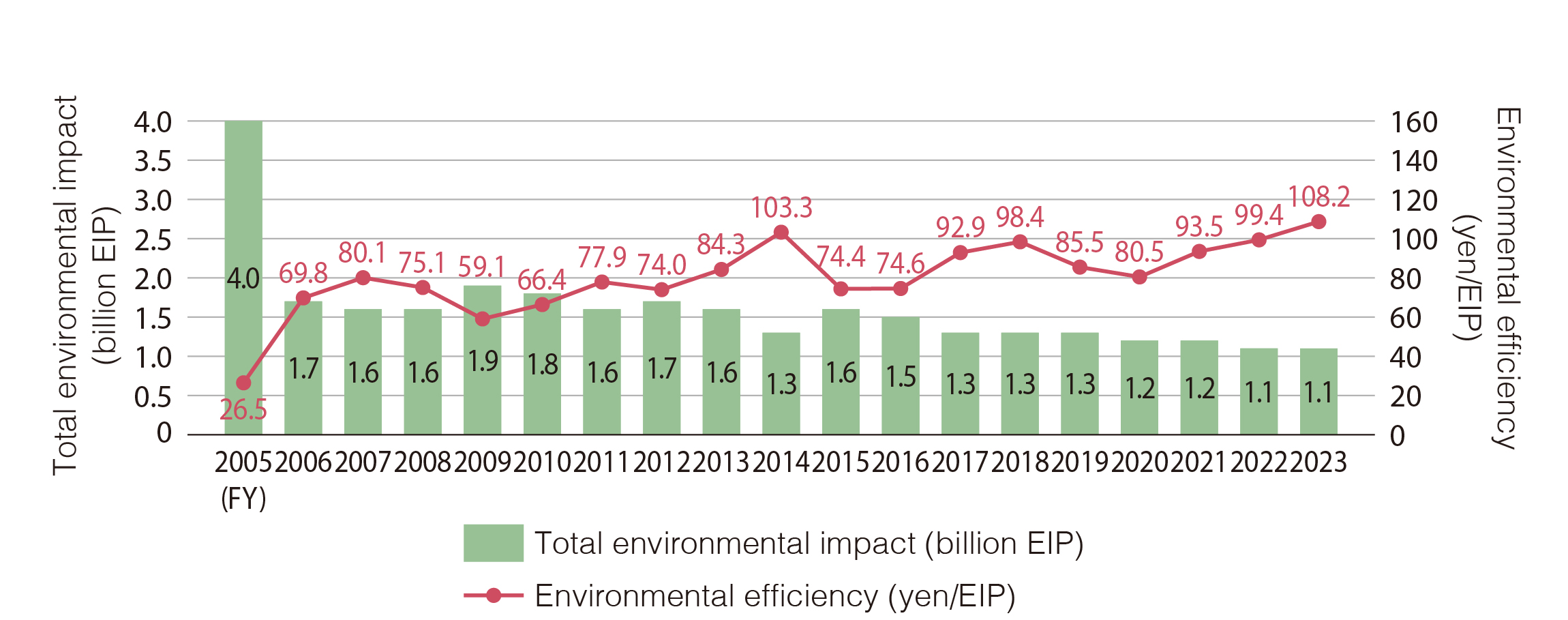
-
Calculated using the JEPIX Simplified Calculation Sheet Ver. 2.0, which is available on JEPIX's website (http://www.jepix.org)
The smaller the total environmental impact, the better, and the greater the environmental efficiency.
Climate Change Related Data
Energy-related data
*Horizontally scrollable
unit | Scope | FY2019 | FY2020 | FY2021 | FY2022 | FY2023 | ||
---|---|---|---|---|---|---|---|---|
Production volume | tons | Domestic | 370,681 | 332,320 | 343,716 | 317,848 | 283,209 | |
Overseas | 201,817 | 238,468 | 179,998 | 149,516 | 162,413 | |||
Total | 572,498 | 570,788 | 523,714 | 467,365 | 445,622 | |||
Raw material input | tons | Domestic | 435,736 | 383,120 | 400,002 | 362,825 | 305,929 | |
Overseas | 267,626 | 319,739 | 236,875 | 198,151 | 206,452 | |||
Total | 703,363 | 702,859 | 636,877 | 560,976 | 512,380 | |||
Energy consumption | Crude oil equivalent kL | Domestic | 90,037 | 81,073 | 81,013 | 78,229 | 64,917 | |
Overseas | 57,322 | 64,981 | 51,205 | 44,993 | 43,072 | |||
Total | 147,358 | 146,054 | 132,218 | 123,221 | 107,989 | |||
Energy consumption intensity per production volume | Crude oil equivalent kL/ton | Domestic | 0.243 | 0.244 | 0.236 | 0.246 | 0.229 | |
Overseas | 0.284 | 0.272 | 0.284 | 0.301 | 0.265 | |||
Total | 0.257 | 0.256 | 0.252 | 0.264 | 0.242 | |||
Energy generated on-site (cogeneration) |
Crude oil equivalent kL | Domestic | 15,894 | 15,975 | 13,165 | 13,332 | 9,878 | |
Overseas | 2,177 | 2,824 | 2,782 | 3,047 | 1,555 | |||
Total | 18,071 | 18,799 | 15,946 | 16,379 | 11,433 | |||
Renewable energy use (solar power generation) |
Crude oil equivalent kL | Domestic | 13 | 12 | 13 | 13 | 5 | |
Overseas | 26 | 30 | 32 | 20 | 11 | |||
Total | 39 | 42 | 45 | 32 | 16 | |||
Energy mix | Purchased electricity | % | Domestic and overseas | 15.2 | 13.0 | 17.1 | 18.4 | 21.3 |
Purchased steam | 32.3 | 30.4 | 33.0 | 33.1 | 31.6 | |||
Fuel oil | 2.2 | 2.0 | 0.8 | 0.5 | 2.1 | |||
Natural gas | 33.8 | 35.6 | 37.6 | 38.1 | 30.7 | |||
LPG | 16.5 | 19.1 | 11.6 | 10.0 | 14.3 |
GHG related data
*Horizontally scrollable
unit | Scope | FY2019 | FY2020 | FY2021 | FY2022 | FY2023 | |
---|---|---|---|---|---|---|---|
GHG emissions*1 | tons CO2 | Domestic | 176,494 | 157,435 | 152,579 | 146,226 | 122,861 |
Overseas | 134,731 | 150,568 | 123,562 | 109,031 | 108,177 | ||
Total | 311,225 | 308,003 | 276,140 | 255,257 | 231,038 | ||
GHG emissions intensity per unit of production | tons CO2/tons | Domestic | 0.476 | 0.474 | 0.444 | 0.460 | 0.434 |
Overseas | 0.668 | 0.631 | 0.686 | 0.729 | 0.666 | ||
Total | 0.544 | 0.540 | 0.527 | 0.546 | 0.518 | ||
CO2 emissions during transport as a consignor*2 | tons CO2 | Domestic | 11,596 | 10,398 | 10,368 | 8,765 | 8,127 |
Increase in CO2 forest absorption*3 | tons CO2 | Domestic | - | 13 | 39 | 11 | 20 |
CO2 reduction by using our products*4 | 10,000 tons CO2 | - | 41.6 | 47.7 | 49.4 | 49.3 | 53.5 |
- Calculated in conformance with the Act on Promotion of Global Warming Countermeasures. However, the CO2 conversion factors for electricity at overseas facilities conforms to the U.S. Energy Information Administration (EIA) figures in the case of the U.S.A., and to the Institute for Global Environmental Strategies (IGES) figures in the case of China, Thailand, and Malaysia.
- Total domestic transportation for Sanyo Chemical Industries, Ltd.; SDP Global Co., Ltd.; and SAN NOPCO LIMITED
- Increase in CO2 absorption by forest thinning and other measures in the town of Wazuka due to funding provided to the Kyoto Model Forest Association's "Forest Creation Fund"
- Calculated by taking the contribution to CO2 reduction by using our products over the use of conventional products and multiplying it by sales for the relevant fiscal year
GHG emissions data by Scope
*Horizontally scrollable
(unit: CO2 tons)
FY2019 | FY2020 | FY2021 | FY2022 | FY2023 | |
---|---|---|---|---|---|
Scope 1 – Direct emissions | 172,349 | 181,509 | 145,753 | 130,031 | 105,287 |
Scope 2 – Indirect emissions from the use of energy supplied by others (market basis) | 138,876 | 126,495 | 130,283 | 125,226 | 125,751 |
Scope 3 – Sum of supply chain emissions across all categories | 2,575,909 | 2,322,571 | 2,393,025 | 2,215,054 | 1,910,981 |
Cat. 1*1 – Purchased goods and services | 1,317,142 | 1,178,559 | 1,216,830 | 1,151,303 | 1,013,918 |
Cat. 2 – Capital goods | 18,974 | 18,367 | 20,922 | 19,670 | 17,065 |
Cat. 3 – Fuel and energy-related activities not included in Scope 1 or 2 | 25,969 | 24,564 | 24,219 | 24,009 | 32,908 |
Cat. 4 – Upstream transportation and distribution | 29,240 | 21,789 | 26,482 | 20,780 | 18,492 |
Cat. 5 – Waste generated in operations | 12,404 | 409 | 812 | 820 | 23,811 |
Cat. 6 – Business travel | 185 | 189 | 184 | 181 | 179 |
Cat. 7 – Employee commuting | 475 | 476 | 472 | 463 | 461 |
Cat. 8*2 – Upstream leased assets | - | - | - | - | - |
Cat. 9*3 – Downstream transportation and distribution | - | - | - | - | - |
Cat. 10*3 – Processing of sold products | - | - | - | - | - |
Cat. 11*3 – Use of sold products | - | - | - | - | - |
Cat. 12*4 – End-of-life treatment of sold products | 1,118,975 | 1,027,575 | 1,055,712 | 948,355 | 749,945 |
Cat. 13*2 – Downstream leased assets | - | - | - | - | - |
Cat. 14*5 – Franchises | - | - | - | - | - |
Cat. 15 – Investments | 52,545 | 50,643 | 47,391 | 49,473 | 54,200 |
- Scope 3 emissions were calculated based on the Basic Guidelines on Accounting for Greenhouse Gas Emissions Throughout the Supply Chain issued by the Ministry of the Environment (https://www.env.go.jp/earth/ondanka/supply_chain/gvc/business/files/ tools/supply_chain.pdf), and by reference to the Ministry of the Environment's Report on Emissions Unit Values for Calculation of Greenhouse Gas Emissions, etc., by Organizations Throughout the Supply Chain. Version 2.3 is used through FY2022, and version 3.4 is used from FY2023
-
[Scope of Calculation]
- Scope 1, Scope 2: Sanyo Chemical Industries, Ltd., domestic affiliates/subsidiaries ((1)-(4) and (10)-(12) in the map at the beginning of this section), and overseas affiliates/subsidiaries ((5)-(9) in the map)
- Scope 3 Cat. 1-7: Sanyo Chemical Industries, Ltd., SDP Global Co., Ltd., San Chemical Co., Ltd.
- Cat. 12: Sanyo Chemical Industries, Ltd., SDP Global Co., Ltd., San Chemical Co., Ltd., certain products sold by overseas affiliates/subsidiaries
- Cat. 15: Sanyo Chemical Industries, Ltd.
- Changed the CO2 conversion factor for purchased raw materials to "IDEA Ver. 2" of the National Institute of Advanced Industrial Science and Technology (AIST) in FY2022 Before FY2021: "Common Unit CO2 Conversion Database ver. 4.01," Ministry of the Environment of Japan, Carbon Footprint System Pilot Project
- Only leases within the group; calculated for Scopes 1 and 2
- Not calculated due to difficulty in collecting necessary data for calculation
- Until FY2021, biomass feedstock was deducted from the total, but from FY2022, the calculation was changed to be done without deduction, and the figures until FY2021 were also revised accordingly. Scope 3 total values were revised accordingly.
- Out of scope as there were no relevant activities
- Scope 3 for FY2022 has been revised due to a flaw in the calculation formula when the emission factor was changed.
Waste and Resource Saving Related Data
*Horizontally scrollable
unit | Scope | FY2019 | FY2020 | FY2021 | FY2022 | FY2023 | |
---|---|---|---|---|---|---|---|
Waste generated | tons | Domestic | 39,363 | 36,627 | 38,274 | 34,587 | 30,653 |
Overseas | 8,302 | 8,803 | 7,891 | 9,607 | 9,371 | ||
Total | 47,665 | 45,430 | 46,165 | 44,194 | 40,024 | ||
Waste intensity per production volume | tons/tons | Domestic | 0.106 | 0.110 | 0.111 | 0.109 | 0.108 |
Overseas | 0.041 | 0.037 | 0.044 | 0.064 | 0.058 | ||
Total | 0.083 | 0.080 | 0.088 | 0.095 | 0.090 | ||
Waste emissions | tons | Domestic | 16,025 | 13,317 | 14,574 | 14,541 | 11,633 |
Overseas | 8,236 | 9,004 | 7,424 | 8,562 | 8,459 | ||
Total | 24,261 | 22,321 | 21,997 | 23,103 | 20,092 | ||
Recycled waste*1 | tons | Domestic | 7,723 | 6,935 | 7,657 | 7,113 | 5,597 |
Overseas | 2,986 | 3,891 | 3,315 | 4,508 | 4,377 | ||
Total | 10,708 | 10,825 | 10,972 | 11,621 | 9,974 | ||
Recycle rate*2 | % | Domestic | 19.6 | 18.9 | 20.0 | 20.6 | 18.3 |
Overseas | 36.0 | 44.2 | 42.0 | 46.9 | 46.7 | ||
Total | 22.5 | 23.8 | 23.8 | 26.3 | 24.9 | ||
Final landfill disposal | tons | Domestic | 3.9 | 0.9 | 1.0 | 2.5 | 0.7 |
Overseas | 7.6 | 3.0 | 5.1 | 3.9 | 3.6 | ||
Total | 11.5 | 3.9 | 6.1 | 6.4 | 4.3 | ||
Landfill rate*3 | % | Domestic | 0.01 | 0 | 0 | 0.01 | 0 |
Overseas | 0.09 | 0.03 | 0.06 | 0.04 | 0.04 | ||
Total | 0.02 | 0.01 | 0.01 | 0.01 | 0.01 | ||
Specially controlled industrial waste*4 | tons | Domestic | 4,383 | 3,689 | 2,016 | 3,295 | 1,259 |
- Total amount of internal and external recycling, including thermal recycling
- Ratio of recycled waste to waste generated: Recycled waste ÷ waste generated×100
- Ratio of final landfill disposal to waste generated: Final landfill disposal ÷ waste generated×100
- Specially controlled industrial waste: Industrial waste with explosive, toxic, infectious, or other properties that may harm human health or the living environment
- Recalculated by applying the changes in domestic waste classifications made in FY2022 retroactively to FY2021 and earlier
Water Resource Related Data
*Horizontally scrollable
unit | Scope | FY2019 | FY2020 | FY2021 | FY2022 | FY2023 | |
---|---|---|---|---|---|---|---|
Tap water usage | thousand ㎥ | Domestic | 143 | 132 | 137 | 139 | 130 |
Overseas | 244 | 263 | 284 | 261 | 204 | ||
Total | 387 | 395 | 421 | 400 | 334 | ||
Ground, surface, and sea water usage | thousand ㎥ | Domestic | 0 | 0 | 0 | 0 | 0 |
Overseas | 0 | 0 | 0 | 0 | 0 | ||
Total | 0 | 0 | 0 | 0 | 0 | ||
Industrial water usage | thousand ㎥ | Domestic | 3,531 | 3,367 | 3,558 | 3,513 | 3,202 |
Overseas | 436 | 507 | 315 | 421 | 437 | ||
Total | 3,967 | 3,873 | 3,874 | 3,933 | 3,639 | ||
Total water usage | thousand ㎥ | Domestic and overseas | 4,354 | 4,269 | 4,295 | 4,333 | 3,973 |
Wastewater emissions | thousand ㎥ | Domestic | 2,894 | 2,738 | 3,039 | 3,024 | 2,711 |
Overseas | 114 | 149 | 132 | 274 | 201 | ||
Total | 3,008 | 2,887 | 3,171 | 3,298 | 2,912 | ||
COD in wastewater | tons | Domestic | 161 | 117 | 156 | 142 | 115 |
Overseas | 29 | 23 | 17 | 29 | 26 | ||
Total | 190 | 140 | 173 | 171 | 142 | ||
Total phosphorus emissions in wastewater | tons | Domestic | 0.62 | 0.83 | 0.77 | 0.97 | 0.68 |
Overseas | 0 | 0 | 0 | 0 | 0.01 | ||
Total | 0.62 | 0.83 | 0.77 | 0.97 | 0.69 | ||
Total nitrogen emissions in wastewater | tons | Domestic | 4.6 | 5.1 | 4.2 | 4.0 | 3.0 |
Overseas | 0.8 | 0.6 | 0.8 | 1.3 | 1.3 | ||
Total | 5.3 | 5.6 | 5.0 | 5.3 | 4.2 |
Wastewater Emissions Area and Environmental Impact (domestic, FY2023)
*Horizontally scrollable
unit | Nagoya Area | Kawasaki Area | Kashima Area | Kyoto Area | Kinuura Area | |
---|---|---|---|---|---|---|
Business site | Nagoya Factory SDP Global Co., Ltd. SAN NOPCO LIMITED |
San Chemical Co., Ltd. |
Kashima Factory San-Petrochemicals Co., Ltd. |
Kyoto Factory Head Office, Head Office Research Laboratory, Katsura Research Laboratory |
Kinuura Factory | |
Emission area | Ise Bay | Tokyo Bay | Sewerage | Sewerage | Sewerage | |
Wastewater emissions | thousand ㎥ | 1,671 | 111 | 788 | 141 | 1 |
COD | tons | 8.7 | 2.4 | 102.8 | 1.4 | 0 |
Total phosphorus | tons | 0.2 | 0 | 0.4 | 0.1 | 0 |
Total nitrogen | tons | 1.3 | 0.3 | 1.3 | 0.1 | 0 |
Chemical Substance Emission Data
Atmospheric emissions related data
*Horizontally scrollable
unit | Scope | FY2019 | FY2020 | FY2021 | FY2022 | FY2023 | |
---|---|---|---|---|---|---|---|
NOx | tons | Domestic | 66 | 87 | 39 | 89 | 84 |
Overseas | 105 | 36 | 20 | 15 | 16 | ||
Total | 171 | 123 | 60 | 104 | 100 | ||
SOx | tons | Domestic | 0.8 | 1.1 | 1.6 | 0.6 | 1.5 |
Overseas | 70.1 | 10.0 | 5.0 | 4.1 | 6.3 | ||
Total | 70.9 | 11.1 | 6.6 | 4.7 | 7.8 | ||
Soot and dust | tons | Domestic | 4.3 | 3.1 | 2.0 | 4.6 | 3.7 |
Overseas | 23.1 | 3.9 | 2.2 | 1.9 | 2.0 | ||
Total | 27.4 | 7.0 | 4.2 | 6.5 | 5.7 | ||
VOC emissions*1 | tons | Domestic | 89 | 70 | 73 | 66 | 44 |
Overseas | 22 | 23 | 17 | 8 | 8 | ||
Total | 112 | 93 | 90 | 74 | 52 | ||
Leakage of CFCs CO2 equivalent Ozone-depleting substances*2 |
kg | Domestic | 184 | 106 | 252 | 102 | 84 |
tons CO2 | 403 | 280 | 827 | 339 | 241 | ||
kg CFC-11 | 0 | 3 | 1 | 1 | 0 |
- Total atmospheric emission of substances subject to former and current revisions of the PRTR Law, and PRTR substances specified by the Japan Chemical Industry Association
- Leakage of HCFCs from air conditioners, chillers, etc. based on the Act on Rational Use and Appropriate Management of Fluorocarbons, converted to CFC-11 equivalent.
Release/Transfer of Substances Subject to the PRTR Law (domestic sites)
(unit: tons)
*Horizontally scrollable
FY2019 | FY2020 | FY2021 | FY2022 | FY2023 | |
---|---|---|---|---|---|
Atmospheric emissions subject to the PRTR Law | 48 | 44 | 47 | 42 | 29 |
Water emissions subject to the PRTR Law | 0.6 | 0.4 | 0.4 | 0.3 | 0.4 |
Transfer of waste subject to the PRTR law | 518 | 365 | 577 | 517 | 361 |
Release and transfer of major substances subject to the PRTR Law, by business site (FY2023)
Substances subject to notification of which at least 0.01 tons of annual emissions were released to the air or water or transferred, or of which at least 0.1 tons were transferred as waste, are listed below.
(unit: tons)
*Horizontally scrollable
Business site | Control No. | Substance | Atmospheric emissions |
Water emissions |
Transfer of waste |
---|---|---|---|---|---|
Nagoya Factory | 1 | Zinc water-soluble compounds | 0 | 0.06 | 0 |
4 | Acrylic acid and its water-soluble salts | 0.30 | 0 | 0 | |
9 | Acrylonitrile | 0.04 | 0 | 0 | |
37 | 4,4'-Isopropylidenediphenol | 0 | 0.02 | 0 | |
53 | Ethylbenzene | 0.12 | 0 | 0 | |
56 | Ethylene oxide | 0.07 | 0 | 0 | |
58 | Ethylene glycol monomethyl ether | 0.06 | 0 | 0 | |
66 | 1,2-Epoxybutane | 0.24 | 0 | 0 | |
68 | 1,2-Epoxypropane (also known as propylene oxide) |
1.47 | 0 | 0 | |
80 | Xylene | 0.07 | 0 | 0 | |
134 | Vinyl acetate | 0.04 | 0 | 0 | |
178 | 1,2-Dichloropropane | 1.12 | 0 | 0.1 | |
232 | N,N-Dimethylformamide | 0.16 | 0.08 | 48.7 | |
300 | Toluene | 3.68 | 0 | 0 | |
398 | Benzyl chloride | 0.03 | 0 | 0 | |
405 | Boron compounds | 0 | 0.04 | 0 | |
674 | Tetrahydrofuran | 0.08 | 0 | 0 | |
737 | Methyl isobutyl ketone | 0.03 | 0 | 0 | |
104 substances Total emissions or |
7.54 | 0.31 | 48.9 | ||
Kashima Factory | 3 | Ethyl acrylate | 0.02 | 0 | 0 |
4 | Acrylic acid and its water-soluble salts | 0.02 | 0 | 0 | |
7 | n-Butyl acrylate | 0.09 | 0 | 0 | |
8 | Methyl acrylate | 0.03 | 0 | 0 | |
53 | Ethylbenzene | 0.77 | 0.02 | 73.8 | |
65 | Epichlorohydrin | 1.51 | 0 | 8.4 | |
80 | Xylene | 0.46 | 0.02 | 49.2 | |
123 | 3-Chloropropene | 0.25 | 0 | 0 | |
128 | Chloromethane | 6.08 | 0 | 0 | |
134 | Vinyl acetate | 0.26 | 0 | 0 | |
157 | 1,2-Dichloroethane | 0.10 | 0 | 1.2 | |
232 | N,N-Dimethylformamide | 0.03 | 0 | 35.7 | |
240 | Styrene | 0.15 | 0 | 1.6 | |
277 | Triethylamine | 0 | 0 | 6.2 | |
300 | Toluene | 0.58 | 0.02 | 0 | |
351 | 1,3-Butadiene | 0.01 | 0 | 0 | |
415 | Methacrylic acid | 0.24 | 0 | 23.2 | |
420 | Methyl methacrylate | 3.93 | 0 | 32.1 | |
511 | Dibenzyl ether | 0 | 0 | 1.5 | |
629 | Cyclohexane | 2.81 | 0 | 0 | |
664 | Organotin compounds | 0 | 0 | 2.4 | |
69 substances Total emissions or |
17.41 | 0.07 | 237.1 | ||
Kyoto Factory | 53 | Ethylbenzene | 0 | 0 | 14.2 |
80 | Xylene | 0 | 0 | 9.5 | |
232 | N,N-Dimethylformamide | 0 | 0 | 33.9 | |
300 | Toluene | 0 | 0 | 5.8 | |
420 | Methyl methacrylate | 0.03 | 0 | 0.7 | |
81 substances Total emissions or |
0.04 | 0 | 64.1 | ||
Kinuura Factory | 56 | Ethylene oxide | 0.06 | 0 | 0 |
68 | 1,2-Epoxypropane (also known as propylene oxide) |
0.19 | 0 | 0 | |
5 substances Total emissions or |
0.25 | 0 | 0 | ||
San Chemical Co., Ltd. | 56 | Ethylene oxide | 0.09 | 0 | 0 |
68 | 1,2-Epoxypropane (also known as propylene oxide) |
0.35 | 0 | 0 | |
39 substances Total emissions or |
0.44 | 0 | 0 | ||
SDP Global Co., Ltd. | 4 | Acrylic acid and its water-soluble salts | 1.66 | 0 | 0.1 |
642 | Didecyldimethylammonium chloride | 0 | 0 | 0.1 | |
3 substances Total emissions or |
1.66 | 0 | 0.2 | ||
SAN NOPCO LIMITED | 4 | Acrylic acid and its water-soluble salts | 0.01 | 0 | 0 |
8 | Methyl acrylate | 0.02 | 0 | 0 | |
53 | Ethylbenzene | 0 | 0 | 1.3 | |
80 | Xylene | 0 | 0 | 0.9 | |
232 | N,N-Dimethylformamide | 0 | 0 | 1.0 | |
300 | Toluene | 0.09 | 0 | 1.2 | |
407 | Polyoxyethylene alkyl ether | 0 | 0 | 0.2 | |
410 | Polyoxyethylene alkyl phenyl ether | 0 | 0 | 0.1 | |
415 | Methacrylic acid | 0.01 | 0 | 0 | |
737 | Methyl isobutyl ketone | 0.01 | 0 | 0 | |
46 substances Total emissions or |
0.16 | 0 | 4.9 | ||
San-Petrochemicals Co., Ltd. | 190 | Dicyclopentadiene | 0.04 | 0 | 0 |
337 | 4-Vinyl-1-cyclohexene | 0.10 | 0 | 0.3 | |
351 | 1,3-Butadiene | 0.22 | 0 | 0 | |
400 | Benzene | 0.05 | 0 | 0 | |
590 | Ethylidene norbornene | 1.09 | 0 | 2.1 | |
7 substances Total emissions or |
1.50 | 0 | 2.4 |
*Horizontally scrollable
Dioxins
(unit: mgTEQ)
Site | Control No. | Substance | Release to air | Release to water | Transfer of waste |
---|---|---|---|---|---|
Nagoya Factory | 243 | Dioxins | 0.52 | 2.73 | 110.64 |
Kyoto Factory | 243 | Dioxins | 0.85 | 0.10 | 1.76 |
*Horizontally scrollable
Atmospheric Emissions of Major Substances Subject to the PRTR Law (domestic sites)
(unit: tons)
Control No. | Substance | FY2001 | FY2019 | FY2020 | FY2021 | FY2022 | FY2023 |
---|---|---|---|---|---|---|---|
4 | Acrylic acid | 4.9 | 11.3 | 10.4 | 5.0 | 6.1 | 2.0 |
9 | Acrylonitrile | 13.0 | 0.1 | 0.1 | 0.1 | 0 | 0 |
53 | Ethylbenzene | 3.8 | 1.2 | 1.1 | 1.2 | 1.2 | 0.9 |
56 | Ethylene oxide | 17.9 | 0.5 | 0.5 | 0.3 | 0.3 | 0.2 |
65 | Epichlorohydrin | 1.0 | 1.6 | 1.4 | 1.4 | 1.4 | 1.5 |
68 | Propylene oxide | 56.2 | 3.7 | 3.3 | 3.4 | 2.3 | 2.0 |
80 | Xylene | 4.6 | 0.7 | 0.6 | 0.7 | 0.7 | 0.5 |
128 | Chloromethane | 9.2 | 13.6 | 17.8 | 17.2 | 15.1 | 6.1 |
157 | 1,2-Dichloroethane | 4.3 | 0.3 | 0.6 | 0.4 | 0.4 | 0.1 |
178 | 1,2-Dichloropropane | 3.0 | 1.1 | 0.8 | 1.0 | 0.9 | 1.1 |
232 | N,N-Dimethylformamide | 2.6 | 0.3 | 0.2 | 0.2 | 0.2 | 0.2 |
240 | Styrene | 1.6 | 0.2 | 0.2 | 0.2 | 0.2 | 0.1 |
300 | Toluene | 30.2 | 0.8 | 0.7 | 8.6 | 5.6 | 4.4 |
351 | 1,3-Butadiene | 3.2 | 0.1 | 0.1 | 0.1 | 0.1 | 0.2 |
420 | Methyl methacrylate | 19.3 | 10.1 | 4.5 | 4.8 | 4.8 | 4.0 |
Main PRTR measures, and VOC emission reduction measures and results
*Horizontally scrollable
Implemented (FY) |
Business site | Measures | Result | Reduction per year (tons) |
---|---|---|---|---|
2001 | Nagoya Factory | Improvement of propylene oxide receiving system | Propylene oxide emissions to the air | 50 |
2001-2005 | San-Petrochemicals Co., Ltd. | Process improvement | Butadiene emissions to the air | 1.4 |
2001-2005 | Nagoya Factory, Kashima Factory | Reduction of chlorinated solvents (process changes, replacements, discontinuations, etc.) | 1,2-Dichloroethane, etc. emissions to the air | 7 |
2002-2004 | Kyoto Factory | Production process improvement and emissions cooling system installation | Methyl methacrylate emissions to the air | 9 |
2002 | Nagoya Factory | Replacement and/or discontinuation | Water soluble hydrogen fluoride emissions to salt water | 0.6 |
2003 | Nagoya Factory | VOC adsorption system installation | Mainly acrylonitrile emissions to the air | 25 |
2004 | San Chemical Co., Ltd. | Propylene oxide emissions combustion system installation | Propylene oxide emissions to the air | 6 |
2005 | Kashima Factory | Production process improvement | Methyl methacrylate emissions to the air | 3 |
2005 | Nagoya Factory | VOC adsorption system installation | Mainly toluene emissions to the air | 17 |
2005 | Nagoya Factory | Ethylene oxide emissions processing system installation | Ethylene oxide emissions to the air | 20 |
2005 | SDP Global Co., Ltd. (Ogaki Production Dept.) | Cyclohexane adsorption/collection system installation | Cyclohexane emissions to the air | 300 |
2006 | Kashima Factory | Cooling system enhancement | Methyl methacrylate emissions to the air | 4 |
2007 | Nagoya Factory | VOC adsorption/collection system installation | Dichloropropane, etc. emissions to the air | 5 |
2007 | Kyoto Factory | VOC adsorption/collection system installation | Ethyl acetate emissions to the air | 12 |
2008 | Nagoya Factory | Cooling system enhancement | Hexane, methyl ethylketone emissions to the air | 12 |
2009 | Nagoya Factory | VOC adsorption/collection system installation | Hexane, methyl ethylketone emissions to the air | 45 |
2010 | Kyoto Factory | VOC removal system installation | Methyl methacrylate emissions to the air | 4 |
2012 | Kinuura Factory | Propylene oxide emissions processing system installation | Propylene oxide emissions to the air | 8 |
2012 | San Chemical Co., Ltd. | Propylene oxide emissions combustion system installation | Propylene oxide emissions to the air | 1.5 |
2015 | Kashima Factory | VOC removal system installation | Ethyl acetate emissions to the air | 150 |
Methyl methacrylate emissions to the air | 18 | |||
2018 | SDP Global Co., Ltd. (Ogaki Production Dept.) | Facility closure | Cyclohexane emissions to the air | 14 |
2020 | Nagoya Factory | Production process improvement, etc. | Propylene oxide emissions to the air | 0.7 |
2020 | Sanyo Kasei (Nantong) Co., Ltd. | VOC combustion/adsorption/collection system installation | Dichloropropane, ethyl acetate, etc. emissions to the air | 9.4 |
2022 | Nagoya Factory, Kashima Factory | Production process improvement | Chloromethane emissions to the air | 9.0 |
2023 | Kashima Factory | Production process improvement | Chloromethane emissions to the air | 1.2 |
Site Report
[Sanyo Chemical domestic facilities]
Nagoya Factory
The Nagoya Factory has our largest production capacity and is located in a coastal industrial zone in South Nagoya. Sanyo Chemical Group companies SAN NOPCO LIMITED and SDP Global Co., Ltd. are also located on the site.
Location | 31-1, Shinpomachi, Tokai, Aichi |
---|---|
Main products | Thermoplastic polyurethane beads for the interior parts of automobiles (TUB), polyurethane products, base materials for electronic materials, surfactants, specialty chemicals |
Started operations | 1968 |
Site area | Approx. 100,000 ㎡ |
ISO certification | ISO9001: obtained in 1998 |
Employees | 291 (as of March 31, 2024) |
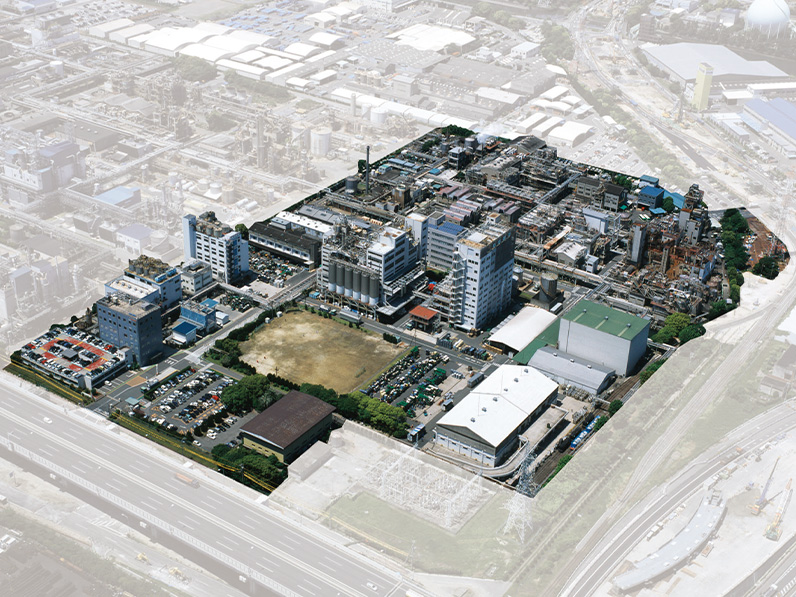
INPUT | |||
---|---|---|---|
Energy | Energy (crude oil equivalent) |
23,100 | kL |
Raw materials | Purchased raw materials and containers | 94,312 | tons |
Water resources | Water intake volume | 2,079 | thousand ㎥ |
Tap water | 36 | thousand ㎥ |
|
Industrial water | 2,043 | thousand ㎥ |
OUTPUT to the environment | ||||
---|---|---|---|---|
Environment | Global environment | GHG (CO2 equivalent) | 49,278 | tons |
Air quality | NOx | 73.7 | tons | |
SOx | 1.3 | tons | ||
Soot and dust | 2.8 | tons | ||
PRTR substances | 7.5 | tons | ||
VOC emissions | 14.7 | tons | ||
Fluorocarbons (CO2 equivalent) | 155 | tons | ||
Water quality | Wastewater | 1,606 | thousand ㎥ | |
COD | 8.7 | tons | ||
Nitrogen | 1.3 | tons | ||
Phosphorus | 0.2 | tons | ||
PRTR substances | 0.3 | tons | ||
Waste | Outsourced waste treatment | 2,445 | tons | |
External recycling | 2,445 | tons | ||
External landfill | 0 | tons | ||
Waste plastics | 458 | tons | ||
PRTR substances | 48.9 | tons | ||
Soil condition | No emissions |
Kinuura Factory
The Kinuura Factory was built for producing alkylene oxide adducts (AOAs) as our third domestic base, following Nagoya Factory and San Chemical Co., Ltd.
Location | 4-43, Nitto-cho, Handa, Aichi |
---|---|
Main products | Raw materials for polyurethane foams |
Started operations | 2010 |
Site area | Approx. 140,000 m² |
ISO certification | ISO9001: obtained in 2010 |
Employees | 20 (as of March 31, 2024) |
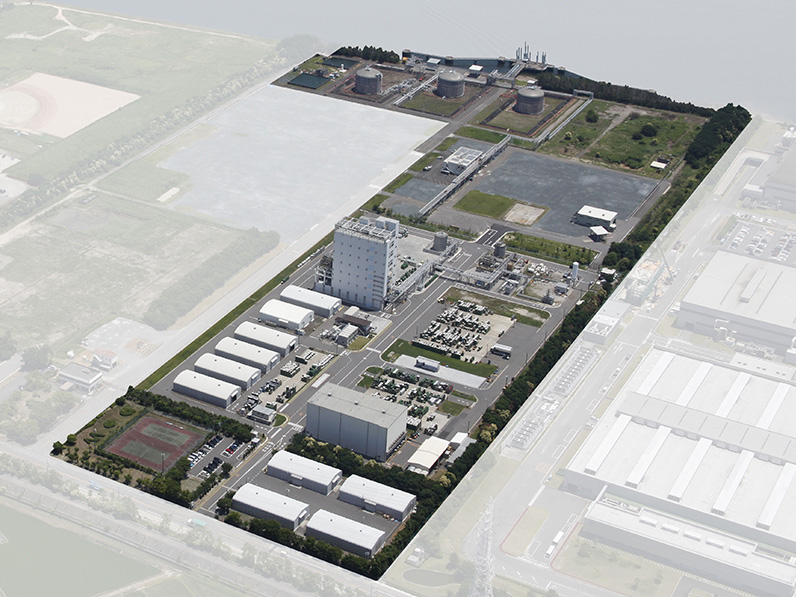
INPUT | |||
---|---|---|---|
Energy | Energy (crude oil equivalent) |
1,083 | kL |
Raw materials | Purchased raw materials and containers | 39,856 | tons |
Water resources | Water intake volume | 40 | thousand ㎥ |
Tap water | 1 | thousand ㎥ |
|
Industrial water | 39 | thousand ㎥ |
OUTPUT to the environment | ||||
---|---|---|---|---|
Environment | Global environment | GHG (CO2 equivalent) | 2,145 | tons |
Air quality | NOx | 0.4 | tons | |
SOx | 0 | tons | ||
Soot and dust | 0 | tons | ||
PRTR substances | 0.3 | tons | ||
VOC emissions | 0.3 | tons | ||
Fluorocarbons (CO2 equivalent) | 0 | tons | ||
Water quality | Wastewater | 1 | thousand ㎥ | |
COD | 0 | tons | ||
Nitrogen | 0 | tons | ||
Phosphorus | 0 | tons | ||
PRTR substances | 0 | tons | ||
Waste | Outsourced waste treatment | 270 | tons | |
External recycling | 270 | tons | ||
External landfill | 0 | tons | ||
Waste plastics | 0 | tons | ||
PRTR substances | 0 | tons | ||
Soil condition | No emissions |
Kashima Factory
Located in industrial park in Ibaraki Prefecture, the Kashima Factory was built in 1976 to serve as Sanyo Chemical's principal production and distribution facility in the Kanto area.
Location | 11-1, Sunayama, Kamisu, Ibaraki |
---|---|
Main products | Polyester beads (PEB) for polymerization toner intermediates, toner resins, lubricant additives, permanent antistatic agents, etc. |
Started operations | 1976 |
Site area | Approx. 130,000 m² |
ISO certification | ISO9001: obtained in 1997 |
Employees | 172 (as of March 31, 2024) |
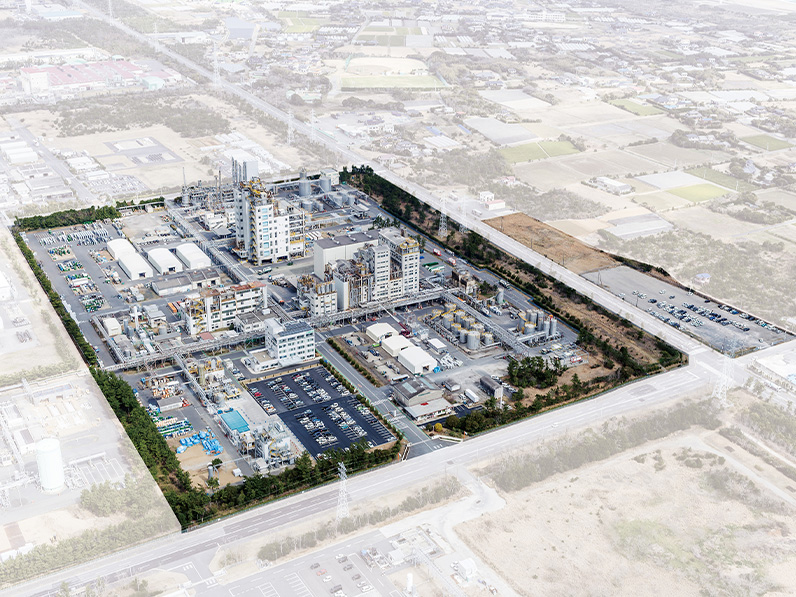
INPUT | |||
---|---|---|---|
Energy | Energy (crude oil equivalent) |
15,518 | kL |
Raw materials | Purchased raw materials and containers | 51,581 | tons |
Water resources | Water intake volume | 672 | thousand ㎥ |
Tap water | 23 | thousand ㎥ |
|
Industrial water | 649 | thousand ㎥ |
OUTPUT to the environment | ||||
---|---|---|---|---|
Environment | Global environment | GHG (CO2 equivalent) | 23,180 | tons |
Air quality | NOx | 0.3 | tons | |
SOx | 0 | tons | ||
Soot and dust | 0.1 | tons | ||
PRTR substances | 17.4 | tons | ||
VOC emissions | 23.7 | tons | ||
Fluorocarbons (CO2 equivalent) | 69 | tons | ||
Water quality | Wastewater | 758 | thousand ㎥ | |
COD | 103 | tons | ||
Nitrogen | 1.3 | tons | ||
Phosphorus | 0.4 | tons | ||
PRTR substances | 0.1 | tons | ||
Waste | Outsourced waste treatment | 3,679 | tons | |
External recycling | 250 | tons | ||
External landfill | 0 | tons | ||
Waste plastics | 627 | tons | ||
PRTR substances | 235.7 | tons | ||
Soil condition | No emissions |
Kyoto Factory
The Kyoto Factory is Sanyo Chemical’s first production facility.
Location | 11-721, Honmachi, Higashiyama-ku, Kyoto |
---|---|
Main products | Lubricant additives, coating and adhesive products, surfactants, etc. |
Started operations | 1949 |
Site area | Approx. 26,000 m² (including the Head Office and Research Laboratory) |
ISO certification | ISO9001: obtained in 1999 |
Employees | 114 (as of March 31, 2024) |
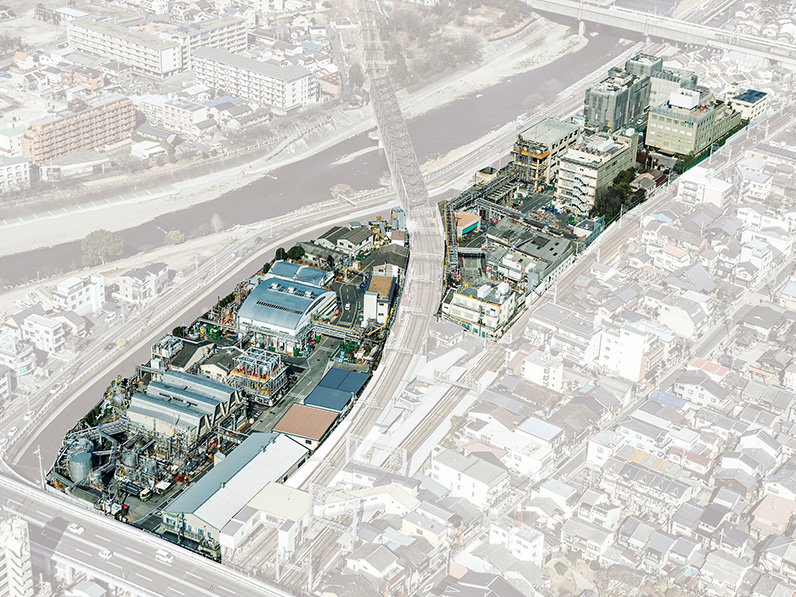
INPUT | |||
---|---|---|---|
Energy | Energy (crude oil equivalent) |
3,779 | kL |
Raw materials | Purchased raw materials and containers | 23,133 | tons |
Water resources | Water intake volume | 184 | thousand ㎥ |
Tap water | 35 | thousand ㎥ |
|
Industrial water | 149 | thousand ㎥ |
OUTPUT to the environment | ||||
---|---|---|---|---|
Environment | Global environment | GHG (CO2 equivalent) | 7,054 | tons |
Air quality | NOx | 2.3 | tons | |
SOx | 0.1 | tons | ||
Soot and dust | 0.2 | tons | ||
PRTR substances | 0 | tons | ||
VOC emissions | 0 | tons | ||
Fluorocarbons (CO2 equivalent) | 13 | tons | ||
Water quality | Wastewater | 126 | thousand ㎥ | |
COD | 1.4 | tons | ||
Nitrogen | 0.1 | tons | ||
Phosphorus | 0.1 | tons | ||
PRTR substances | 0 | tons | ||
Waste | Outsourced waste treatment | 3,661 | tons | |
External recycling | 63 | tons | ||
External landfill | 0 | tons | ||
Waste plastics | 37 | tons | ||
PRTR substances | 64.1 | tons | ||
Soil condition | No emissions |
Head Office, Head Office Research Laboratory, Katsura Research Laboratory
Our Head Office and main R&D facility. The research & development departments of SDP Global Co., Ltd. and San-Apro Ltd. are also located here.
Location | Head Office and Head Office Research Laboratory: 11-1, Ikkyo Nomoto-cho, Higashiyama-ku, Kyoto Katsura Research Laboratory: 1-40, Goryo Ohara, Nishikyo-ku, Kyoto |
---|---|
On-site offices | Sanyo Chemical Industries, Ltd. Head Office, Head OfficeResearch Laboratory, Katsura Research Laboratory, SAN NOPCO LIMITED, San-Apro Ltd., and SDP Global Co., Ltd. |
Employees | Head Office and Head Office Research Laboratory: 450, Katsura Research Laboratory: 109 (as of March 31, 2024) |
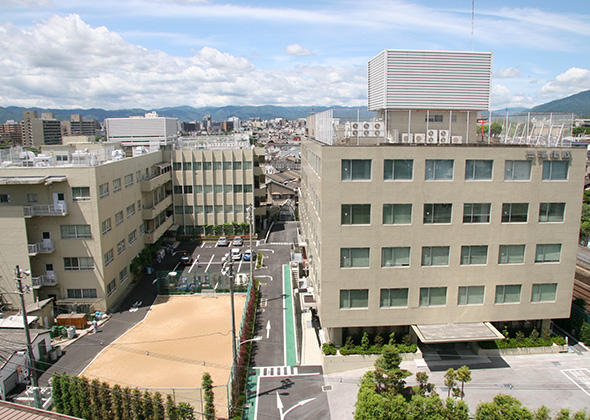
Head Office, Head Office Research Laboratory
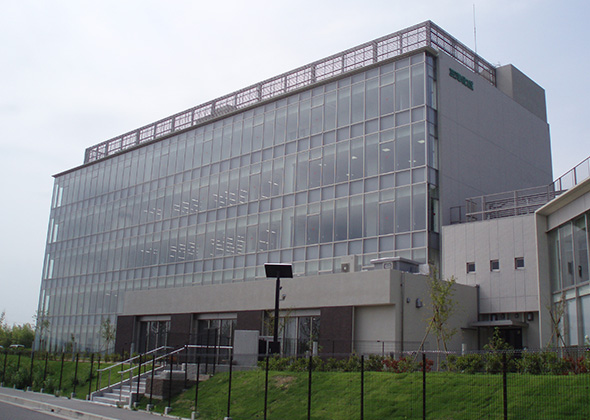
Katsura Research Laboratory
INPUT | |||
---|---|---|---|
Energy | Energy (crude oil equivalent) |
1,495 | kL |
Water resources | Water intake volume | 15 | thousand ㎥ |
Tap water | 15 | thousand ㎥ |
|
Industrial water | 0 | thousand ㎥ |
OUTPUT to the environment | ||||
---|---|---|---|---|
Environment | Global environment | GHG (CO2 equivalent) | 2,904 | tons |
Air quality | NOx | 0 | tons | |
SOx | 0 | tons | ||
Soot and dust | 0 | tons | ||
PRTR substances | 0.01 | tons | ||
VOC emissions | 0.05 | tons | ||
Fluorocarbons (CO2 equivalent) | 4 | tons | ||
Water quality | Wastewater | 15 | thousand ㎥ | |
COD | 0 | tons | ||
Nitrogen | 0 | tons | ||
Phosphorus | 0 | tons | ||
PRTR substances | 0 | tons | ||
Waste | Outsourced waste treatment | 180 | tons | |
External recycling | 129 | tons | ||
External landfill | 0 | tons | ||
Waste plastics | 0 | tons | ||
PRTR substances | 4.3 | tons | ||
Soil condition | No emissions |
[Domestic Subsidiaries and Affiliates]
SDP Global Co., Ltd.
SDP Global Co., Ltd.'s Nagoya Factory is a specialized manufacturer of superabsorbent polymers. SDP Group consists of SDP Global Co., Ltd. in Japan, San-Dia Polymers (Nantong) Co., Ltd. in China and SDP GLOBAL (MALAYSIA) SDN. BHD. in Malaysia. Production will cease and the company will be dissolved during FY2024.
Location | 31-1, Shinpomachi, Tokai, Aichi |
---|---|
Main products | Superabsorbent polymers (SAPs) |
Established | 2001 |
ISO certification | ISO9001: obtained in 2000 |
Employees | 20 (as of March 31, 2024) |
INPUT | |||
---|---|---|---|
Energy | Energy (crude oil equivalent) |
8,154 | kL |
Raw materials | Purchased raw materials and containers | Combined with Sanyo Chemical Nagoya Factory | |
Water resources | Water intake volume | 67 | thousand ㎥ |
Tap water | 1 | thousand ㎥ |
|
Industrial water | 67 | thousand ㎥ |
OUTPUT to the environment | ||||
---|---|---|---|---|
Environment | Global environment | GHG (CO2 equivalent) | 15,945 | tons |
Air quality | NOx | 2.8 | tons | |
SOx | 0 | tons | ||
Soot and dust | 0.4 | tons | ||
PRTR substances | 1.7 | tons | ||
VOC emissions | 1.7 | tons | ||
Fluorocarbons (CO2 equivalent) | 0 | tons | ||
Water quality | Wastewater | Combined with Sanyo Chemical Nagoya Factory | ||
COD | ||||
Nitrogen | ||||
Phosphorus | ||||
PRTR substances | 0 | tons | ||
Waste | Outsourced waste treatment | 402 | tons | |
External recycling | 402 | tons | ||
External landfill | 0 | tons | ||
Waste plastics | 1.7 | tons | ||
PRTR substances | 0.2 | tons | ||
Soil condition | No emissions |
SAN NOPCO LIMITED
In 1966, it was established as a joint venture between Nopco Chemical Company of the United States and Sanyo Chemical Industries, Ltd. of Japan. At present, it is a wholly owned subsidiary of Sanyo Chemical.
Website | https://www.sannopco.co.jp/eng/ |
---|---|
Location | 31-1, Shinpomachi, Tokai, Aichi |
Main products | Manufacture and sale of industrial agents for pulp & paper, paints, latex, ceramics, and electronics |
Established | 1966 |
ISO certification | ISO9001: obtained in 2000 |
Employees | 87 (as of March 31, 2024) |
INPUT | |||
---|---|---|---|
Energy | Energy (crude oil equivalent) |
1,797 | kL |
Raw materials | Purchased raw materials and containers | 16,809 | tons |
Water resources | Water intake volume | 85 | thousand ㎥ |
Tap water | 3 | thousand ㎥ |
|
Industrial water | 81 | thousand ㎥ |
OUTPUT to the environment | ||||
---|---|---|---|---|
Environment | Global environment | GHG (CO2 equivalent) | 4,249 | tons |
Air quality | NOx | 0 | tons | |
SOx | 0 | tons | ||
Soot and dust | 0 | tons | ||
PRTR substances | 0.2 | tons | ||
VOC emissions | 1.2 | tons | ||
Fluorocarbons (CO2 equivalent) | 0 | tons | ||
Water quality | Wastewater | 65 | thousand ㎥ | |
COD | 0 | tons | ||
Nitrogen | 0 | tons | ||
Phosphorus | 0 | tons | ||
PRTR substances | 0 | tons | ||
Waste | Outsourced waste treatment | 42 | tons | |
External recycling | 9 | tons | ||
External landfill | 0 | tons | ||
Waste plastics | 12 | tons | ||
PRTR substances | 4.9 | tons | ||
Soil condition | No emissions |
San Chemical Co., Ltd.
Jointly established with Nippon Oil Corporation (now ENEOS Corporation) in 1982. As a specialized manufacturer of raw materials for polyurethane foam, polyethylene glycol, etc., it took over the Kawasaki Factory, the Sanyo Chemical Industries, Ltd.'s second AOA factory in Japan, which started operations in 1960.
Website | http://www.san-chemical.com/ |
---|---|
Location | Head Office and Kawasaki Factory: 13-2, Chidori-cho, Kawasaki-ku, Kawasaki |
Main products | Raw materials for polyurethane foam, raw materials for detergents, perfume and cosmetics, etc. |
Established | 1982 |
ISO certification | ISO9001: obtained in 2000 |
Employees | 41 (as of March 31, 2024) |
INPUT | |||
---|---|---|---|
Energy | Energy (crude oil equivalent) |
3,167 | kL |
Raw materials | Purchased raw materials and containers | 64,045 | tons |
Water resources | Water intake volume | 128 | thousand ㎥ |
Tap water | 14 | thousand ㎥ |
|
Industrial water | 115 | thousand ㎥ |
OUTPUT to the environment | ||||
---|---|---|---|---|
Environment | Global environment | GHG (CO2 equivalent) | 6,264 | tons |
Air quality | NOx | 0 | tons | |
SOx | 0 | tons | ||
Soot and dust | 0 | tons | ||
PRTR substances | 0.4 | tons | ||
VOC emissions | 0.9 | tons | ||
Fluorocarbons (CO2 equivalent) | 0 | tons | ||
Water quality | Wastewater | 111 | thousand ㎥ | |
COD | 2.4 | tons | ||
Nitrogen | 0.3 | tons | ||
Phosphorus | 0 | tons | ||
PRTR substances | 0 | tons | ||
Waste | Outsourced waste treatment | 914 | tons | |
External recycling | 878 | tons | ||
External landfill | 1 | tons | ||
Waste plastics | 14 | tons | ||
PRTR substances | 0 | tons | ||
Soil condition | No emissions |
San-Petrochemicals Co., Ltd.
A 50:50 joint venture between Sanyo Chemical and ENEOS Corporation, and a global leading specialized manufacturer of ENB.
Website | https://www.san-petrochemicals.com/en/ |
---|---|
Location | 11-2, Sunayama, Kamisu, Ibaraki |
Main products | EPDM rubber materials such as ENB (ethylidene norbornene) |
Established | 1977 |
Employees | 39 (as of March 31, 2024) |
INPUT | |||
---|---|---|---|
Energy | Energy (crude oil equivalent) |
6,555 | kL |
Raw materials | Purchased raw materials and containers | 16,193 | tons |
Water resources | Water intake volume | 61 | thousand ㎥ |
Tap water | 2 | thousand ㎥ |
|
Industrial water | 59 | thousand ㎥ |
OUTPUT to the environment | ||||
---|---|---|---|---|
Environment | Global environment | GHG (CO2 equivalent) | 11,322 | tons |
Air quality | NOx | 4.5 | tons | |
SOx | 0.1 | tons | ||
Soot and dust | 0.3 | tons | ||
PRTR substances | 1.5 | tons | ||
VOC emissions | 1.7 | tons | ||
Fluorocarbons (CO2 equivalent) | 0 | tons | ||
Water quality | Wastewater | 30 | thousand ㎥ | |
COD | 0.3 | tons | ||
Nitrogen | 0 | tons | ||
Phosphorus | 0 | tons | ||
PRTR substances | 0 | tons | ||
Waste | Outsourced waste treatment | 41 | tons | |
External recycling | 41 | tons | ||
External landfill | 0 | tons | ||
Waste plastics | 6 | tons | ||
PRTR substances | 2.4 | tons | ||
Soil condition | No emissions |
San-Apro Ltd.
Website | https://www.san-apro.co.jp/eng/ |
---|---|
Location | Research laboratory: 1-40, Goryo Ohara, Nishikyo-ku, Kyoto Sales office : Tokyo |
Lines of business | Manufacture and sale of DBU and DBN extremely strong basic organic compounds, urethane catalysts, epoxy resin curing accelerators, photo acid generators, water soluble rust inhibitors, etc. |
Established | 1966 |
ISO certification | ISO9001: obtained in 2003 |
Employees | 34 (as of March 31, 2024) |
San-Apro researches, develops, and sells products specialized for catalysts. As a fabless company, it does not have an in-house production facility but commissions manufacturing to other companies, including Sanyo Chemical.
The company was established in 1966 as a joint venture with U.S.-based Abbott. Later, in 1986, the venture partner changed to U.S.-based Air Products, and the company name was changed to “San-Apro.”
In 2017, Germany-based Evonik took over the business of Air Products. At present, San-Apro is a 50:50 joint venture of Sanyo Chemical and Evonik.
Sanyo Chemical Logistics Co., Ltd.
Location | Head Office: 31-1, Shinpomachi, Tokai, Aichi Business offices: Kyoto, Nagoya, Kashima, Kawasaki |
---|---|
Lines of business | Warehousing, shipping, loading and unloading in factories, and forwarding of Sanyo Chemical Group products |
Established | 2020 |
Sanyo Chemical Logistics was established in 2020 through the merger of Nagoya Sanyo Warehouse Co., Ltd., which handled product storage and shipping as well as cargo handling on the premises for Sanyo Chemical Group, and Sanyo Transport Co., Ltd., which mainly handled the transportation of Sanyo Chemical products. The company aims to increase operational efficiency, reduce transportation costs, and improve overall logistics services by centralizing functions related to the supply chain.
Shiohama Chemicals Warehouse Co., Ltd.
Location | 2-2-6 Yako, Kawasaki-ku, Kawasaki, Kanagawa |
---|---|
Lines of business | Warehousing, loading, unloading, and forwarding for hazardous goods |
Established | 1983 |
A 50:50 joint venture of Sanyo Chemical and ENEOS corporation, this warehouse company located near San Chemical Co., Ltd. handles San Chemical products.
Overseas Subsidiaries and Affiliates
San-Dia Polymers (Nantong) Co., Ltd.
San-Dia Polymers (Nantong) is a Chinese subsidiary of SDP Global Co., Ltd., a specialized manufacturer of superabsorbent polymers. A transfer of equity during FY2024 is currently being considered.
Location | Nantong, Jiangsu, China |
---|---|
Lines of business | Manufacture and sale of superabsorbent polymers |
Established | 2003 |
ISO | ISO9001: obtained in 2007 ISO14001: obtained in 2013 |
Employees | 166 (as of March 31, 2024) |
INPUT | |||
---|---|---|---|
Energy | Energy (crude oil equivalent) |
27,098 | kL |
Raw materials | Purchased raw materials and containers | 149,976 | tons |
Water resources | Water intake volume | 365 | thousand ㎥ |
Tap water | 71 | thousand ㎥ |
|
Industrial water | 294 | thousand ㎥ |
OUTPUT to the environment | ||||
---|---|---|---|---|
Environment | Global environment | GHG (CO2 equivalent) | 72,882 | tons |
Air quality | NOx | 14.9 | tons | |
SOx | 5.9 | tons | ||
Soot and dust | 1.7 | tons | ||
VOC emissions | 2.9 | tons | ||
Water quality | Wastewater | 42 | thousand ㎥ | |
COD | 2.1 | tons | ||
Nitrogen | 0.3 | tons | ||
Phosphorus | 0 | tons | ||
Waste | Outsourced waste treatment | 1,026 | tons | |
External recycling | 591 | tons | ||
External landfill | 0 | tons | ||
Soil condition | No emissions |
SDP GLOBAL (MALAYSIA) SDN. BHD.
This is a production site in Southeast Asia for SDP Global Co., Ltd., a specialized manufacturer of superabsorbent polymers. Production will cease and the company will be dissolved in March 2024.
Location | Johor, Malaysia |
---|---|
Lines of business | Manufacture and sale of superabsorbent polymers |
Established | 2015 |
Employees | 72 (as of March 31, 2024) |
INPUT | |||
---|---|---|---|
Energy | Energy (crude oil equivalent) |
11,004 | kL |
Raw materials | Purchased raw materials and containers | 40,092 | tons |
Water resources | Water intake volume | 118 | thousand ㎥ |
Tap water | 118 | thousand ㎥ |
|
Industrial water | 0 | thousand ㎥ |
OUTPUT to the environment | ||||
---|---|---|---|---|
Environment | Global environment | GHG (CO2 equivalent) | 21,704 | tons |
Air quality | NOx | 0.5 | tons | |
SOx | 0.3 | tons | ||
Soot and dust | 0.3 | tons | ||
VOC emissions | 0 | tons | ||
Water quality | Wastewater | 12 | thousand ㎥ | |
COD | 0.5 | tons | ||
Nitrogen | 0 | tons | ||
Phosphorus | 0 | tons | ||
Waste | Outsourced waste treatment | 1,008 | tons | |
External recycling | 730 | tons | ||
External landfill | 0 | tons | ||
Soil condition | No emissions |
Sanyo Kasei (Thailand) Ltd.
Sanyo Kasei (Thailand) is our base of operations in the ASEAN region.
Website | https://www.sanyo-kasei.co.th/EN/home.html |
---|---|
Location | Head Office: Bangkok, Thailand Factory: Rayong, Thailand |
Lines of business | Manufacture and sale of textile chemicals, surfactants, papermaking chemicals, paint and ink resins, etc. |
Established | 1997 |
ISO | ISO9001: obtained in 2004 ISO14001: obtained in 2009 |
Employees | 92 (as of March 31, 2024) |
INPUT | |||
---|---|---|---|
Energy | Energy (crude oil equivalent) |
1,686 | kL |
Raw materials | Purchased raw materials and containers | 5,114 | tons |
Water resources | Water intake volume | 142 | thousand ㎥ |
Tap water | 0 | thousand ㎥ |
|
Industrial water | 142 | thousand ㎥ |
OUTPUT to the environment | ||||
---|---|---|---|---|
Environment | Global environment | GHG (CO2 equivalent) | 3,778 | tons |
Air quality | NOx | 0.4 | tons | |
SOx | 0.2 | tons | ||
Soot and dust | 0 | tons | ||
VOC emissions | 3.1 | tons | ||
Water quality | Wastewater | 118 | thousand ㎥ | |
COD | 20 | tons | ||
Nitrogen | 0.9 | tons | ||
Phosphorus | 0 | tons | ||
Waste | Outsourced waste treatment | 2,612 | tons | |
External recycling | 184 | tons | ||
External landfill | 0 | tons | ||
Soil condition | No emissions |
Sanyo Kasei (Nantong) Co., Ltd.
Sanyo Kasei (Nantong) is our production base in China. Production will cease and the company will be dissolved in March 2024.
Location | Nantong, China |
---|---|
Lines of business | Manufacture of textile chemicals, surfactants, papermaking chemicals, paint and ink resins, etc. |
Established | 2003 |
ISO | ISO9001: obtained in 2006 ISO14001: obtained in 2012 |
Employees | 97 (as of March 31, 2024) |
INPUT | |||
---|---|---|---|
Energy | Energy (crude oil equivalent) |
2,929 | kL |
Raw materials | Purchased raw materials and containers | 10,017 | tons |
Water resources | Water intake volume | 15 | thousand ㎥ |
Tap water | 15 | thousand ㎥ |
|
Industrial water | 0 | thousand ㎥ |
OUTPUT to the environment | ||||
---|---|---|---|---|
Environment | Global environment | GHG (CO2 equivalent) | 9,111 | tons |
Air quality | NOx | 0 | tons | |
SOx | 0 | tons | ||
Soot and dust | 0 | tons | ||
VOC emissions | 1.5 | tons | ||
Water quality | Wastewater | 27 | thousand ㎥ | |
COD | 3.2 | tons | ||
Nitrogen | 0.1 | tons | ||
Phosphorus | 0 | tons | ||
Waste | Outsourced waste treatment | 3,764 | tons | |
External recycling | 2,825 | tons | ||
External landfill | 0 | tons | ||
Soil condition | No emissions |
Sanyo Chemical Texas Industries, LLC
Sanyo Chemical Texas Industries is a production base for urethane beads for automobile interior parts (upholstery materials) in the United States.
Location | Pasadena, Texas, USA |
---|---|
Lines of business | Manufacture of thermoplastic polyurethane beads |
Established | 2005 |
Employees | 12 (as of March 31, 2024) |
INPUT | |||
---|---|---|---|
Energy | Energy (crude oil equivalent) |
355 | kL |
Raw materials | Purchased raw materials and containers | 1,253 | tons |
Water resources | Water intake volume | 0.5 | thousand ㎥ |
Tap water | 0.1 | thousand ㎥ |
|
Industrial water | 0.3 | thousand ㎥ |
OUTPUT to the environment | ||||
---|---|---|---|---|
Environment | Global environment | GHG (CO2 equivalent) | 701 | tons |
Air quality | NOx | 0 | tons | |
SOx | 0 | tons | ||
Soot and dust | 0 | tons | ||
Water quality | Wastewater | 1.9 | thousand ㎥ | |
COD | 0 | tons | ||
Nitrogen | 0 | tons | ||
Phosphorus | 0 | tons | ||
Waste | Outsourced waste treatment | 50 | tons | |
External recycling | 47 | tons | ||
External landfill | 3 | tons | ||
Soil condition | No emissions |